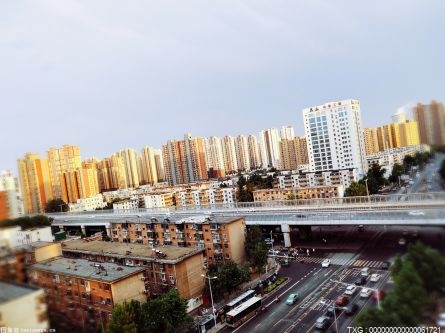
现阶段以铅酸电池电动车为主,锂电池渗透率逐渐提升
中国两轮电动车在储能类型上分为三类:铅酸电池、锂电池、氢能源。目前,市面上销售的两轮电动车以铅酸电池为主, 具备技术成熟,价格便宜,可回收利用率高等特点;锂电池在两轮电动车中的渗透率不足10%,其主要原因有:1)锂电 池技术门槛高,研发成本高;2)锂电池产业链不完善,回收以及售后服务环节不足;3)消费者价格敏感,对锂电池动力 的需求不够强烈。与铅酸电池相比,锂电池拥有寿命长、质量轻、绿色环保、能量密度大等优点,在新国标的促进作用下, 锂电池在两轮电动车中的渗透率有望进一步提高。此外,氢能源电池两轮车产品也在积极的探索与研发中,未来也将成为中国两轮车市场的重要组成部分。
(相关资料图)
根据“新国标”技术规范,两轮电动车分为三类 《电动自行车安全技术规范》(GB17761-2018) 强制性国家标准出台后,长期以来不明确的“电动车”“电动踏板车”被 重新定义,根据《新国标》技术规范,两轮电动车可划分为三类:电动自行车、电动轻便摩托车、电动摩托车。电动自行 车:又称国标车,要求必须具备脚踏骑行功能,蓄电池作为辅助能源,速度不超过25km/h,属于非机动车。电动轻便摩托 车:由电力驱动,电机额定功率总和不大于4KW,最高设计车速不大于 50km/h的摩托车,属于机动车。电动摩托车:由 电力驱动,电机额定功率总和大于4KW,最高速度大于50km/h的摩托车,属于机动车。
2020年中国两轮电动车行业规模达1046亿元 2020年,中国两轮电动车市场规模达1046亿元,2021-2023年两轮电动车的规模增长贡献主要来自新国标替换产生的销量 增长。新国标后,低端两轮电动车产品被淘汰,两轮电动车产品平均单价有所提升,预计2022年两轮电动车市场规模可达 1443亿元。
锂电池能量密度一般为120-180wh/kg,显著高于铅酸电池28-40wh/kg。锂电池符合新国标轻量化需求,以雅迪小叮当系列为例, 铅酸电池重量17kg,远高于锂电池4.7kg。铅酸版车型若要满足新国标要求,除电池外其他部件重量不能超过40公斤,这就需要考 虑将车型的尺寸减小或采用轻型材料设计,而轻型材料往往售价高昂。锂电池另一大优势在于体积小、可拆卸提出,方便用户充电, 还能降低电池被盗风险。
电池管理系统设计概述:
电池管理系统大的方向讲,在电动汽车和混合动力汽车中必不可少,必须对电池进行检测,才能保证电池正常充放电,防止过充和过放,延长使用寿命,保证续航里程。
锂电池能量密度高,电池内部化学物质活性强。当电芯出现过充、过放等非正常使用时,极有可能出现电池损坏,极端情况下,还会导致起火和爆炸。因此,锂电池需要有一套监控系统,随时监控锂电池的电压,电流等参数,一旦超过事先设定的阈值,则直接关断电池主回路。
两轮电动车BMS 行业内成为两轮电动车电池保护板
保护板分为硬件板与软件板
所谓硬件板,就是保护板上没有可以进行编程的芯片,只是按照特定的线路进行连接,保护板的参数是固定的。这一类保护板一般成本较低,功能简单,很难实现逻辑上的特殊控制要求。而软件板则是在硬件板的基础上,加了可以编程的芯片,因此这类保护板除了实现基本功能以外,还能实现很多特殊的功能。只要通过修改程序和添加外设,基本可以实现任何功能。比如远程引爆车辆中的锂电池。
分口与同口保护板
保护板为了现实保护电池的功能,必须要能够主动切断电池主回路。因此,在电池包内部,电池的主回路是要经过保护板的。为了对充电和放电都能进行控制,保护板必须具有两个开关,分别控制充电和放电回路(姑且这么理解)。在同口保护板中,这两个开关串在一条线上,接到电池包外部,充电和放电都经过此线。而在分口保护板中,电池分出两根线,分别接充电开关和放电开关,再接到电池外部。
之所以会出现同口和分口保护板,是为了降低成本:一般电动车锂电池包的充电电流要比放电电流小,如果两个开关串到一条线上,那么两个开关就得照着大的买。而分口的话,充电电流小,就可以用一个更小的开关。这里说的开关,其实就是MOSFET,是锂电保护板的主要成本,而且国内相关产品技术受限,核心部件需要进口。
按照串数和持续放电电流大小来分
串数比较好理解,常见的7串(三元24v),13串(三元48v),17串(三元60v),20串(三元72v)。保护板需要采集每一串电芯的电压,因此串数不同,保护板是不同的。而电流大小,就是决定了如上所说开关的大小(MOS数量),对价格的影响很重。
铁锂常见的就是 15/16串48v, 20串60v ,24串72v。我公司就是只做铁锂,因为铁锂更安全,有更长的寿命,适合出口。当然我们在国内的销售额也很好。
锂电池体积小、可拆卸提出,方便用户充电,
降低电池被盗风险。
最后就是按照电芯材料来分不同的电芯材料,放电截止电压和充电截止电压是不一样的。因此,所使用的保护板也是不一样的,最常见的就是三元保护板和磷酸铁锂保护板,一般三元电芯电压范围为2.7-4.2v,而磷酸铁锂则是2.5-3.6v。
他们的主要功能
过充电压、过充保护延时、过充恢复电压过放电压、过放保护延时、过放恢复电压
下面,我们来看电流保护相关的参数。保护板的电流保护,一方面是防止充电电流太大,另一方面是防止放电电流太大。过大的电流,会伤害电池,也可能烧坏保护板自身。首先,保护板有一个基本的关键参数:放电电流和充电电流。该电流是保护板的持续放电或者充电电流,它代表了保护板自己的载流能力,和电池无关。除了该参数以外,保护板还有一对电流参数,即充电保护电流和放电保护电流。顾名思义,就是在充电或者放电过程中,电流超过该值的大小就关断。同之前的道理一样,电流的保护也是有延时的,不过电流保护的恢复是自动的,只要电流减小就会自动恢复。
现在,我们又多了两组共4个数据和一对单独的数据:
放电过流保护电流大小、放电过流保护延时充电过流保护电流大小、充电过流保护延时持续放电电流、持续充电电流
短路保护,同过流保护一样,当电流超过设定值时切断回路。也有延时控制功能。不过恢复模式有两种,主动恢复和被动恢复。
电流检测和短路保护,需要选择合适的电流传感器。我们可以把电流检测分为几个范围:
1,检测5A到70A的直流或交流电流。
检测5A到50A的直流或交流电一般选用芯片式的霍尔电流传感器,比如
CH701电流传感器IC,是工业、汽车、商业和通信系统中交流或直流电流传感的经济而精确的解决方案。小封装是空间受限应用的理想选择,同时由于减少了电路板面积而节省了成本。典型应用包括电机控制、负载检测和管理、开关电源和过电流故障保护。 参考文章:霍尔传感器芯片该如何选型
CH701可以检测到50A峰值的电流。
如果需要检测更大电流,需要更高的隔离电压,可以选择更大电流范围的产品,比如16脚的CH701W系列,电流范围可以到70A,绝缘耐压可以到4800Vrms:
2,检测50A到200A的直流或交流电流。
可以选用直插型的电流传感器
CH704 是专为大电流检测应用开发的隔离集成式电流传感芯片。CH704 内置 0.1 mΩ 的初级导体电阻,有效降低芯片发热支持大电流检测:±50A, ±100A, ±150A, ±200A。其内部集成独特的温度补偿电路以实现芯片在 -40 到150度全温范围内良好的一致性。出厂前芯片已做好灵敏度和静态(零电流)输出电压的校准,在全温度范围内提供 ±2% 的典型准确性。
参考文章:意瑞半导体推出250A霍尔电流传感器产品,可以替换Allegro的ACS758/ACS770/ACS772
温度保护,温度保护分上限温度和下限温度,当温度超出该范围时,保护板关断电池。不同的保护板功能不一,有些只有高温保护,有些高低温都有。而有些可以设置充电和放电不同的保护温度。这主要是和保护板所使用的芯片有关。关于具体的东西,后面会更详细的说一下。
上面,我们说了保护板的电压过充和过放保护,电流过流和短路保护,温度高低温保护。其中电压、电流保护,高温保护是保护板的基本功能,前两项更是必不可少的,高温保护也相对比较重要。下面,我们就来说说保护板的自身参数,比如自耗电和内阻等,他们不起保护作用,但是对电池的性能是有影响的。
自耗电
自耗电分为工作自耗电和静态(睡眠)自耗电,保护板自耗电的电流一般是ua级别。工作自耗电电流较大,主要为保护芯片、mos驱动等消耗。保护板的自耗电太大会过多消耗电池电量,如果长时间搁置的电池,保护板自耗电可能导致电池亏电。
保护板的主回路内阻也是一个很重要的参数,保护板的主回路内阻主要来源于pcb板上铺设阻值,mos的阻值(主要)和分流电阻的阻值。在保护板进行充放电时,特别是mos部分,会产生大量的热,因此一般保护板的mos上都需要贴一大块的铝片用于导热和散热。
好了,上面就是一个保护板的基本功能和参数了,除了这些基本功能以外,为了使用不同的应用场景个需求,保护板还有各种各样的附加功能(如均衡),特别是带软件的保护板中,功能更是异常丰富,比如蓝牙、wifi、GPS、串口、CAN等应有尽有,再高阶一点,就成了电池管理系统了(BMS)。
锂电池保护板电流选择
1.锂电池保护板电流是由保护IC检测电压和MOS管内阻决定的,如果保护IC无法更改,可以改MOS管,比如DW01与8205MOS,用一颗MOS管是2~5A,用两颗MOS管并联电流就会增加一倍。现在的大容量移动电源有的用3~4颗MOS管并联。
2.保护板保护电流=过流检测电压/MOS管内阻(由于是两颗MOS管串联,计算时MOS管内阻要乘2)
3.锂电池选保护板要根据电池的容量来定
锂电池保护板选购要点
为了保护锂电池组寿命,建议任何时候电池充电电压都不要超过3.65v,就是锂电池保护板保护电压不高于3.65v,均衡电压建议3.4v-3.5v,电池放电保护电压一般2.5v以上就可以。
充电器建议最高电压为3.5串数,自放电越大,均衡需要时间越长,自放电过大的电芯已经很难均衡,需要剔除。所以挑选锂电池保护板的时候,尽量挑选3.6v过压保护的,3.5v左右启动均衡的。
总之锂电池保护板的内阻越低越好,越低越不发热。保护板限流大小是靠康铜丝取样电阻决定的,但持续电流能力是mos决定的
储能电池管理系统(ESBMS)与动力电池管理系统(BMS)的不同之处
储能电池管理系统,与动力电池管理系统非常类似。但动力电池系统处于高速运动的电动汽车上,对电池的功率响应速度和功率特性、SOC估算精度、状态参数计算数量,都有更高的要求。
储能系统规模极大,集中式电池管理系统与储能电池管理系统差异明显,这里只拿动力电池分布式电池管理系统与其对比。
2.1电池及其管理系统在各自系统里的位置有所不同
在储能系统中,储能电池在高压上只与储能变流器发生交互,变流器从交流电网取电,给电池组充电;或者电池组给变流器供电,电能通过变流器转换成交流发送到交流电网上去。
储能系统的通讯,电池管理系统主要与变流器和储能电站调度系统有信息交互关系。一方面,电池管理系统给变流器发送重要状态信息,确定高压电力交互情况;另一方面,电池管理系统给储能电站的调度系统PCS发送最全面的监测信息。
电动汽车的BMS,在高压上,与电动机和充电机都有能量交换关系;在通讯方面,与充电机在充电过程中有信息交互,在全部应用过程中,与整车控制器有最为详尽的信息交互。如下图所示。
2.2硬件逻辑结构不同
储能管理系统,硬件一般采用两层或者三层的模式,规模比较大的倾向于三层管理系统。
动力电池管理系统,只有一层集中式或者两分布式,基本不会出现三层的情况。小型车主要应用一层集中式电池管理系统。两层的分布式动力电池管理系统,如下图所示。
从功能看,储能电池管理系统第一层和第二层模块基本等同于动力电池的第一层采集模块和第二层主控模块。储能电池管理系统的第三层,则是在此基础上增加的一层,用以应对储能电池巨大的规模。
打一个不是那么恰当的比方。一个管理者的最佳下属数量是7个人,如果这个部门一直扩张,出现了49个人,那么只好7个人选一个组长,再任命一个经理管理这7个组长。超越个人能力,管理容易出现混乱。
映射到储能电池管理系统上,这个管理能力就是芯片的计算能力和软件程序的复杂度。
2.3通讯协议有区别
储能电池管理系统与内部的通讯基本都采用CAN协议,但其与外部通讯,外部主要指储能电站调度系统PCS,往往采用互联网协议格式TCP/IP协议。
动力电池,所在的电动汽车大环境都采用CAN协议,只是按照电池包内部组件之间使用内部CAN,电池包与整车之间使用整车CAN做区分。
2.4储能电站采用的电芯种类不同,则管理系统参数区别较大
储能电站出于安全性及经济性考虑,选择锂电池的时候,往往选用磷酸铁锂,更有的储能电站使用铅酸电池、铅碳电池。而电动汽车目前的主流电池类型是磷酸铁锂电池和三元锂电池。
电池类型的不同,其外部特性区别巨大,电池模型完全不可以通用。而电池管理系统与电芯参数必须是一一对应的关系。不同厂家出品的同一种类型的电芯,其详细参数设置也不会相同。
2.5阈值设置倾向不同
储能电站,空间比较富裕,可以容纳较多的电池,但某些电站地处偏远,运输不便,电池的大规模更换,是比较困难的事情。储能电站对电芯的期望是寿命长,不要出故障。基于此,其工作电流上限值会设置的比较低,不让电芯满负荷工作。对于电芯的能量特性和功率特性要求都不需要特别高。主要看性价比。
动力电池则不同,在车辆有限的空间内,好不容易装下的电池,希望把它的能力发挥到极致。因此,系统参数都会参照电池的极限参数,这样的应用条件对电池是恶劣的。
2.6两者要求计算的状态参数数量不同
SOC是两者都需要计算的状态参数。但直到今天,储能系统并没有一个统一要求,储能电池管理系统到底必须哪些状态参数计算能力。再加上,储能电池的应用环境,空间相对充裕,环境稳定,小偏差在大系统里不易被人感知。因此,储能电池管理系统的计算能力要求相对低于动力电池管理系统,相应的单串电池管理成本也没有动力电池高。
2.7储能电池管理系统应用被动均衡条件比较好
储能电站对管理系统均衡能力的要求非常迫切。储能电池模组的规模比较大,多串电池串联,较大的单体电压差将造成整个箱体的容量下降,串联电池越多,其损失的容量越多。从经济效率角度考虑,储能电站很需要充分的均衡。
又由于在充裕的空间和良好的散热条件下,被动均衡能够更好的发挥效力,采用比较大的均衡电流,也不必担心温升过高问题。低价的被动均衡,可以在储能电站大展拳脚。
编辑:黄飞
标签: