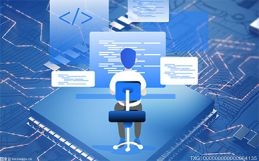
回顾过去五六十年,先进逻辑芯片性能基本按照摩尔定律来提升。 提升的主要动力来自三极管数量的增加来实现,而单个三极管性能的提高对维护摩尔定律只是起到辅佐的作用。 随着SOC的尺寸逐步逼近光罩孔极限尺寸(858mm2)以及制程的缩小也变得非常艰难且性价比遇到挑战, 多芯片封装技术来到了舞台的中心成为进一步提升芯片性能的关键。 覆晶键合技术已然成为先进多芯片封装最重要的技术之一。
尽管某些基于晶圆级或者面板级扇出型封装的工艺流程可以不用到覆晶封装,但是这个技术方向有其自己的应用局限性。 比如其目前量产重布线层的层数大多在五层以内,使其不太适合服务器芯片的封装。 如今最常见的基于焊球的覆晶键合封装技术一共有三种:回流焊(mass reflow), 热压键合(Thermo Compression Bonding or TCB)和激光辅助键合(Laser Assisted Bonding, or LAB)。 基于铜铜直接键合的覆晶封装不在这个文章的讨论重点,我们会在后续的文章中讨论目前最具希望能进一步缩小的bump间距(bump pitch scaling down)的方法,比如混合键合(Hybrid bonding)和铜铜直接热压键合等等。
热压键合工艺的基本原理与传统扩散焊工艺相同,即上下芯片的Cu 凸点对中后直接接触,其实现原子扩散键合的主要影响参数是温度、压力、时间. 由于电镀后的Cu 凸点表面粗糙并存在一定的高度差,所以键合前需要对其表面进行平坦化处理,如化学机械抛光(chemical mechanical polishing,CMP),使得键合时Cu 表面能够充分接触. 基于目前研究文献,通过热压键合工艺实现Cu-Cu 低温键合的方法从机理上可分为两类,即提高Cu 原子扩散速率和防止/减少待键合Cu 表面的氧化.
(资料图片仅供参考)
表一在high level总结了这三种基于焊球的覆晶键合封装技术的优缺点。 可以看到没有一种键合方式是完美的。 对于某个产品来说,任务是要找到最合适的键合方法。 作为本文的重点,热压键合最大的优势是对die和基板(可以是substrate, another die or wafer or panel)的更为精准的控制。
表一:基于焊球的覆晶键合技术
接下来我们着重讨论一下高端的逻辑芯片的键合方式为什么逐步从回流焊键合过渡到热压键合。 图一(a)给出了一种常见的回流焊芯片键合流程。 先将芯片上的bumps沾上助焊剂(flux)或者在基板上的C4 (controlled-collapse chip connection)区域喷上定量的助焊剂。 然后用贴片设备将芯片相对比较精准地放到基板上。 然后将芯片(die)和基板整体放到一个回流焊炉子里。 常见的回流焊的温度控制由图一(b)给出。 整个回流焊的时间通常在5到10分钟。 虽然时间很长,但因为这是批量处理,一个回流焊炉同时可以容纳非常大量的加工产品。 所以整体的吞吐量还是非常高的,通常可以达到每小时几千颗芯片的产量,或者更高。
根据所使用的回流锡膏的种类,回流温度的峰值一般控制在240ºC到260ºC。 在回流键合后通常我们需要去除助焊剂和加CUF (Capillary Underfill毛细管底部填充料)来填充bump之间的空隙来提供产品的可靠性。 常见的回流焊过程中,我们不对芯片和基板做过多限制。 这导致芯片和基板的曲翘得不到有效的控制,使得在芯片与基板之间的距离(chip gap height)在芯片面下的变化非常大。 过大的曲翘导致NCO(noncontacted opening 虚焊)和SBB(solder ball bridging 桥接)这两类最为常见的缺陷。 基于回流焊的复杂多芯片键合的良品率可能非常的低,使得回流焊不再是最合适的键合方式。
回流焊芯片键合的良品率跟诸多因素有关,常见的有芯片大小和厚度,bump间距(pitch),基板的厚度,热膨胀系数(CTE)的不匹配(mismatch),如图二所示。 同时bump pitch的进一步减小也进一步增加SBB的概率。 另外值得指出的是,即使没有发生NCO和SBB缺陷,过大的chip gap height变化和过大的曲翘对下游的封装步骤也带来了巨大的挑战。
图一:常见的回流焊芯片键合流程
图二:常见的回流焊芯片键合的良品率和芯片大小和厚度的关系
图三给出了常见的热压键合bonder的结构。 基板和芯片都有各自的加热装置。 取决于锡膏的种类,通常基板会被加150ºC到200ºC之间。 基板被真空束缚在非常平整的基座上,从而基板的曲翘得到了很好地控制。 芯片同样被真空束缚在非常平整的bond head上,相应的芯片的曲翘也得到了很好地控制。
芯片和基板之间的对准需要非常精准,其中包括XY平面内的alignment,芯片和基板之间距离(Z方向上的控制)以及相对的倾斜(tip tilt)。 通常alignment的精度要求要达到±3 µm 3 sigma的要求。 键合区域的氧气浓度过高会对键合产生不利影响,比如孔洞(voids)的形成从而影响键合强度。 区别于回流焊的5到10分钟的时长,热压键合整个过程大概只需要在1秒到5秒之间。 但是由于热压键合是一个芯片一个芯片的键合而不是像回流焊那样批量进行的,所以热压键合的吞吐量大约只有回流焊的1/5。 加上热压键合的设备通常比回流焊的设备要贵不少,这两个原因导致热压键合的成本比回流焊键合要高。
另外,因为键合所需的热量主要由bonder head的加热器所提供,C4的热量会向基板边缘扩散。 这导致在C4边缘要比中心温度低不少。 这使得热压键合的峰值温度要远超锡膏的融化温度通常在300°C以上。 跟回流焊峰值温度相比,过高的热压键合温度给键合材料的选取,键合工艺的稳定性以及产品的可靠性带来不小的挑战。
前面提到回流焊键合,由于熔融的锡膏为了降低表面能从而有自校正的能力,这个能力能够帮助芯片的bumps在回流焊后更准确的跟基板的bumps对准。 然后在热压键合中,由于芯片和基板在锡膏熔融状态下都被束缚着,因此失去这个优势。 好在目前绝大多数的热压键合设备对芯片和基板相对的放置精度可以做得非常好,有些可以达到±2 μm 精度with 3σ。 ASM Pacific,Kulicke&Soffa,Besi以及Toray等是目前最常见的热压键合设备供应商。
目前国产设备商也是积极布局该领域,例如华封,唐人制造等等。 各个厂商的热压键合设备可以有各自的特色,但是他们的设备都在以下方面进行各种优化:位置控制精度,倾斜/并行度控制精度, 快速且精确的温度控制,精准的bonding force的测量和控制,芯片和基板的真空吸附控制,设备的稳定性,同一型号设备差异性的减少,产能(throughput)的提高,设备成本的下降,设备占地面积的减少等等。
图三:常见的热压键合bonder的结构
基于回流焊和热压键合的chip gap height (CGH)差异性在图四中给出。 对这个特定的产品来说,基于回流焊键合的产品的CGH范围从70 µm到100 µm ,如此大的CGH variation使得键合的加工窗口(process margin)非常低。 只要来料的差异性稍大,就可能导致生产良品率的下降。 相比之下,基于热压键合的产品的CGH变化范围大约只有5µm。 小的CGH variation不仅能帮助提高键合本身的process margin,而且能帮助减少下游封装测试流程中的来料的差异性从而使得下游的封测步骤更稳定。
图四:基于回流焊和热压键合的Chip gap height
接下来,我们大概地讲一下最常见的TCCUF (Thermo compression boding with Capillar UnderFill)热压键合步骤流程,整个过程通常在1-5秒
将基板真空吸附到非常平整的pedestal上,并通常加热到150ºC到200ºC。 将基板的温度设定尽可能的高来减少键合时间。
在基板的C4区域喷涂上足量的助焊剂 。
将bond head加热到150ºC到200ºC之间,并用bond head去Pick up芯片。
用up-looking和down-looking相机来确定芯片和基板的相对位置,通过校准过的算法算出芯片所需的空间位置调整来完全对照基板的bumps,通过设备上精密的机械控制来完成这个步骤。
然后将bond head连带吸附的芯片一起以sub um的精度靠近基板。 此时芯片和基板都处在锡球融化温度以下,所以锡球都是固体。 锡球可以是在基板上也可以在芯片上或者两者都有。
在下降过程中bond head一直处在压力敏感控制,既进行着非常灵敏且实时的力测量。
当芯片和基板接触的那瞬间,系统探测到一个压力上的变化,从而判断接触发生同时迅速将 bond head从压力敏感控制转为压力和位置共同控制。
此时通过bond head上的加热装置迅速将芯片加热至300ºC以上。 值得指出的是热压键合的温度变化率一般都是在100 ºC/s。 相比之下,回流焊键合的温度变化率要低很多,通常在2 ºC/s。
当锡球处于熔融状态时,通过bond head对芯片的精确位置控制来确保每对bumps都键合上,且将chip gap height控制在合理的范围内。 值得指出的是,在加热的过程中,真个系统都会热膨胀,这部分的膨胀需要bond head位置的精确控制来抵消。
将bond head的温度迅速冷却至锡球熔点以下,使得锡球变为固相。 通常冷却温度变化率要比加热温度变化率要低一些,通常在−50 °C/s。
关闭bond head对芯片的真空吸附,芯片跟bond head分离。 芯片键合在基板上移出热压键合设备,键合完成。
为了更好地说明热压键合关键步骤,我们用下图的一个bonding profile作为一个例子来进一步解释。 事实上,基于不同的产品,bonding profiles可以非常不同。 所有这些bonding profiles的实现都基于热压键合设备对温度,压力,位置等的精确控制。 如图五(a)所示,红线,蓝线和黑线分别代表bond head的温度,压力,位移随时间的曲线。 当bond head探测到压力变化就说明芯片和基板已经触碰,迅速将芯片和基板加热到锡球熔点以上。 对于通常的SAC305锡球(96.5% Sn, 3% Ag, and 0.5% Cu),这个温度大约要到300 °C以上。 由于巨大的温度梯度,即使C4中心的bumps可能已经在300°C以上了,但是在C4边缘的锡球可能勉强的锡球熔点以上。
正是这个原因,通常bond head的峰值温度要远高于锡球熔点。 图中蓝线显示在加热过程中,bond head是处在恒定压力控制模式直到锡球融化。 由于锡球融化压力瞬间下降,取决于所选择的chip gap height,此时bond head由原来的压力可能变成拉伸力。 此时我们调整bond head的高低位置来保持恒定压力控制,这个位置的调整也可以用来弥补整个设备的热膨胀带来的影响。 通常我们会在探测到锡球融化后,继续将芯片向下压5到10μm。 这么做的主要原因是solder bumps的高低并不一致,通常coplanarity可能就在5到10 μm这个范围。 Bond head可能会继续下压更多来确保没有NCO(on-contact open). 随后Bond head也可能上升来将chip gap height控制在一个合理的范围内。 然后bond head迅速降温至锡球熔点以下来完成键合。
图五:热压键合的bonding profile, 已经键合过程
根据填充材料的不同,热压键合又可以分为TCNCF(Thermo compression boding with Non Conductive Film), TCNCP(Thermo compression boding with Non Conductive Paste), TCCUF(Thermo compression boding with Capillar UnderFill), TCMUF(Thermo compression boding with Molded UnderFill)等等。 取决于基板材料的不同,热压键合又可以分为Chip-to-Substrate (C2S) and Chip-to-Wafer (C2W) ,Chip-to-Chip (C2C) 和Chip-to-Panel. 我们将在今后的文章中进一步讨论这些。
审核编辑:汤梓红
标签: